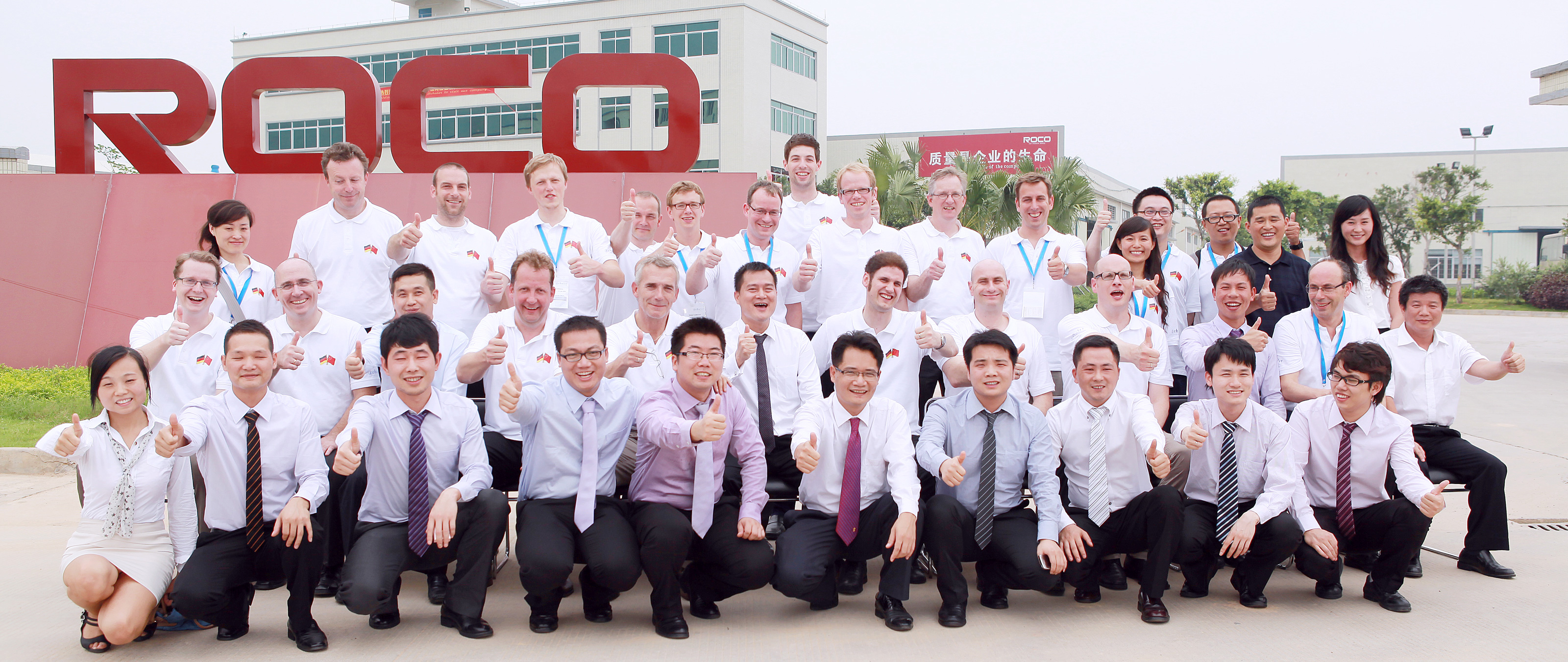
Produktionsentwicklung: Roco
Kleiderschränke, Wandverbauten, Wandregale, Tische und Betten in Melaminausführung – das alles produziert der Möbelhersteller Roco mit Sitz in Guangzhou für den chinesischen Markt. Roco führt zwar einen Produktkatalog, jedoch wird jedes Möbel für den Kunden individuell nach seinen Wunschmaßen gefertigt. Zudem bietet Roco 18 unterschiedliche Melamindekore an. Die Konsequenz für die Fertigung: Eine extrem hohe Varianz an verschiedenen Teilen und Farben.
Als man 2011 in das neue Werk investierte, entschied man sich für einen Maschinenpark, der nahezu komplett aus Maschinen der HOMAG Group besteht. Dazu gehören vier Plattenaufteilsägen HPP 180 von HOLZMA, zwei HOMAG Kantenanleimmaschinen KAL 210, zwei Kantenanleimmaschinen eines chinesischen Herstellers (später ersetzt durch zwei Kantenanleimmaschinen HOMAG KAL 310), zwei CNC-Bohrmaschinen von WEEKE vom Typ PTP 160 (gebaut bei HOMAG Machinery Shanghai), eine BHX 050 von WEEKE und fünf 3-Kopf-Bohrmaschinen.
Vor dem Hintergrund dieser eher ökonomischen und einfachen Maschinentechnik stellte sich für Roco die zentrale Frage: Wie erreicht das Unternehmen eine maximale Leistung bei auftragsbezogener Fertigung, mit Einsatz eines Maschinenparks aus Standardmaschinen mit begrenzten Optionen? Gefertigt wurde bisher im Zweischichtbetrieb – hier erreichte man eine Anzahl von rund 80 Schränken pro Tag.
So nahm man die Berater von SCHULER Consulting ins Boot. Gemeinsam mit dem Projektteam des Kunden erarbeitet man eine komplett neue Ablauforganisation für Roco. Das Ziel: Mindestens die gleiche Menge an Teilen in nur einer Schicht zu produzieren. Nach eingehender Analyse der vorherrschenden Produktionsbedingungen setzte man die erste Maßnahme um: Die komplette Schließung der zweiten Schicht.
Im nächsten Schritt fasste man die Aufträge einer Woche zusammen und filterte diese nach einem speziellen Kriterium, beispielsweise nach Produkt (Schrank, Bett, Tisch) und Farbe (Dekor). Hieraus ergab sich eine definierte Reihenfolge im Zuschnitt.
Platzbedingt – und da sich auch keine weiteren Vorteile bei größeren Losgrößen ergaben – wurden immer 20 Aufträge der gleichen Farbe zusammengefasst und für den Zuschnitt optimiert.
In einem festgelegten Wochenrhythmus arbeitet das Team bei Roco heute nun die unterschiedlichen Farben (Dekore) und deren entsprechende Aufträge ab. Bei Aufträgen mit Teilen in den Hauptfarben werden heute alle Sägen mit der gleichen Farbe zur gleichen Zeit mit jeweils 20 optimierten Aufträgen gestartet. Ebenfalls neu: Die Mitarbeiter an den Sägen stellen die Teile nach einem definierten Schema in die bereitstehenden Kommissionierboxen.
Für den Zuschnitt hat das folgenden Effekt: Die Materialbereitstellung für die Sägen erfolgt auf die Minute genau und Wartezeiten für einen möglichen Dekorwechsel an den Sägen existieren nicht mehr.
Ebenso entfallen beim Kantenanleimen Stillstandzeiten bedingt durch Kantenwechsel. Der gesamte Wochenpulk eines Dekors kommt hintereinander zum Bekanten. Durch das definierte Bereitstellen der Teile in den Kommissionierboxen gelingt eine nahtlose Beschickung der Kantenanleimmaschinen. Für die Qualitäts- und Vollständigkeitskontrolle der Werkstücke sorgt im Anschluss ein eigenständiger Bereich.
Ein Engpassbereich liegt bei Roco im Prozessschritt „Bohren“. Hier machte man es sich zur Aufgabe, die Werkstücke je nach Anforderung und Position der Bohrlöcher auf die verschiedenen Maschinen aufzuteilen. „Welche Maschine kann was am besten und am schnellsten?“
Entsprechend wurden Teilegruppen für jede Bohrmaschine definiert und durch geschulte Fachkräfte an der Qualitätskontrolle markiert. Durch den zunehmenden Mengenausstoß waren die vorhandenen Bohrmaschinen schnell an den Kapazitätsgrenzen angelangt. So wurde in eine zusätzliche CNC-Bohrmaschine investiert. Eingesetzt werden Bohrer von Leuco. Hier ließ sich Roco schnell von der Qualität deutscher Produkte überzeugen. Ausgerissene Bohrlöcher gehören nun der Vergangenheit an.
Um ein höheres Qualitätsniveau zu erreichen, ersetzte man im gleichen Zug die beiden chinesischen Kantenanleimmaschinen durch aufgerüstete und flexible Maschinen vom Typ HOMAG KAL 310. Positiver Nebeneffekt: Die Energiekosten sind um nahezu 50 % gesunken – bei doppeltem Ausstoß pro Schicht.
Fazit: Betrachtet man die Leistungsdaten VOR der Analyse und der Umsetzung der neuen Maßnahmen, so erreichte man in zwei Schichten beim Kantenanleimen 1.800 Takte. HEUTE fertigt Roco in einer Schicht beim Kantenanleimen mit einem Ausstoß von 3.400 Takten. Das entspricht nahezu einer Vervierfachung des Ausstoßes in knapp drei Monaten durch das SCHULER-Team.
„Die Professionalität und die engagierte Arbeitsweise von SCHULER haben mich sehr beeindruckt. So konnten wir, insbesondere durch die Unterstützung des SCHULER Mitarbeiters Klaus Kellner im Jahre 2012 bei gleichem Arbeitseinsatz ein Vielfaches unseres Produktionsausstoßes erreichen. Diesen erfolgreichen Weg werden wir auch in Zukunft zusammen mit SCHULER weitergehen und gemeinsam unsere neu gesteckten Ziele erreichen“ so Vincent Wu, CEO von Roco.