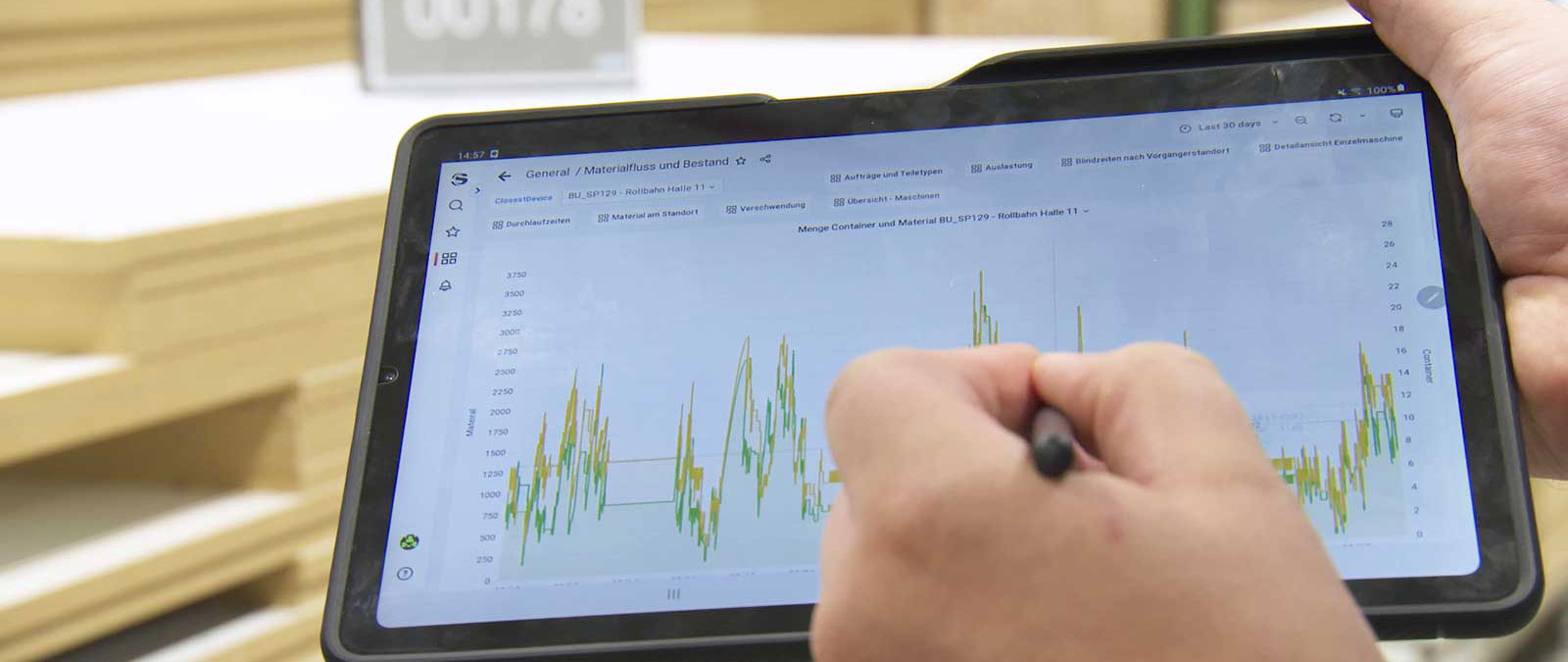
Production Visualisation Digital Value Stream Optimization
Production Visualisation Digital Value Stream Optimization
A service based on beacons and smartphones
"The weakest process determines the production output." What's the problem? To identify this process in your production, you first need one thing: lots of data. Fast moving parts, very short throughput times and different types of machines of different ages make production data collection in the wood and furniture industry a challenge. If you wanted to know the processes in your production, you used to send an employee with a stopwatch into the production hall. A costly and time-consuming undertaking that no longer meets the complex requirements of today's productions. Get to know digital value stream optimisation here!
Benefits
- Plug-and-play installation of hardware and software without an IT project.
- A tool that evaluates your material and goods flows based on digital traces
- A paperless system to find your materials in real time
- XaaS - everything as a service - with hardware, software and platform that you can rent according to your needs
- Value stream optimisation based on key performance indicators, e.g. inventory, labour minutes, yield, etc.
- Concrete optimisation of the value stream in your production by SCHULER
- You receive standard values for processing times, for more precise production scheduling and production control, as a basis for piecework wages and for cost planning.
- Combined with your machine hourly rate, you now have your process costs at component level
Images
Technical Data
Times, costs and values become visible
At SCHULER Consulting, we use digital technologies for data collection as part of a value stream analysis: By using common smartphone technology, it is already possible to collect production data regardless of the machine type, manufacturer or application area - and without a great deal of personnel effort or high implementation costs. Based on the collected data, we identify redundant and cost-intensive processes and develop targeted optimisation measures for your value stream.
Technical and methodological requirements
A set consisting of proven calculation methodology, Bluetooth low energy beacons and smartphones provides you with everything you need to know the actual value-added time in your production and to implement optimisation measures in a targeted manner. In production, the smartphone takes over the external sensory monitoring of the machines and workplaces. It does not have any software interfaces and can therefore run completely externally. In interaction with the Bluetooth LE beacons, it can, for example, localise the stacks in a production. Using our calculation methodology, this hardware and software set can be used to collect a lot of machine and operational data with almost no employee interaction. The technology works for any machine and in any production context, whether furniture, kitchen, shop or timber construction.
Finding every stack of material in production at the touch of a button, viewing the progress of current orders, receiving target and processing times as well as automatically generated unit costs is thus no longer just wishful thinking, but the next step towards complete production transparency.
Here's how your colleagues produce
Videos
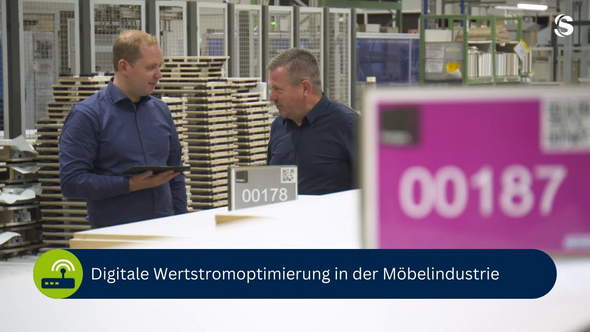
Please confirm that when you use YouTube, data such as your IP address, browser identifier and similar may be transmitted to Google.
» Privacy Policy
Digitale Wertstromoptimierung bei Burger Küchen
Volle Transparenz über Wertstrom und Intralogistik
Brochures
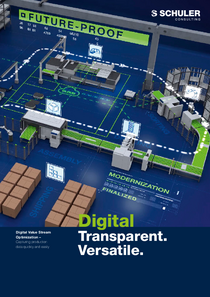