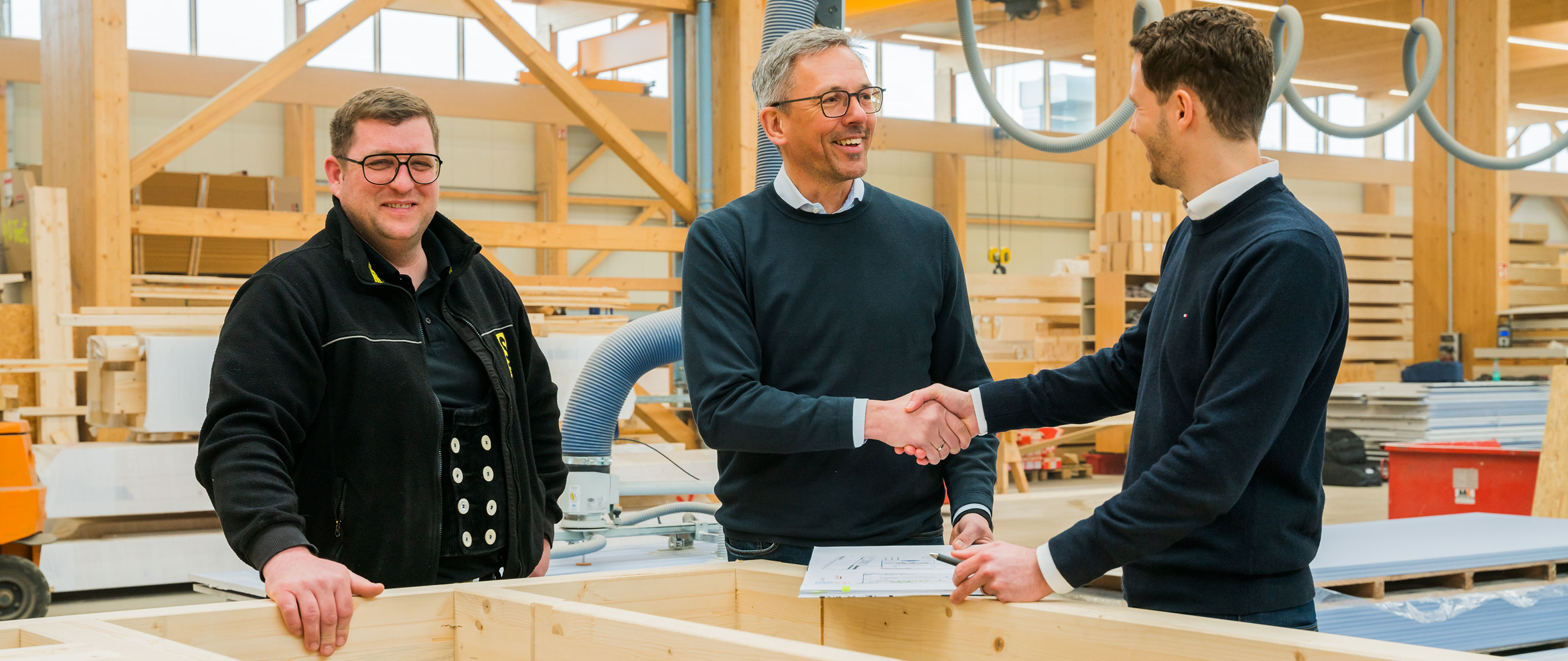
The story of special construction experts "Gebr. Schütt KG" (Brothers Schütt company) is one of growth: founded more than 130 years ago as a carpentry business, the Schütt family established a glue-laminated wood production business in the 1960s and, over the following decades, have developed this business into a construction company that is active across the whole of Germany, with its own architects and engineers. Today, the company is taking the step into industrial production, with the help of its employees and the support of SCHULER Consulting. Tillmann Schütt, fifth-generation managing director of the company, and Michael Postulart, consultant at SCHULER Consulting, talk about small successes, big changes and the important role of employees on this journey.
Interview by Dr. Stefan Bockel.
Mr. Schütt, your company is currently developing from a large carpentry business to an industrial construction company. Why did you decide to involve the consulting company SCHULER Consulting to accompany you on this journey?
Tillmann Schütt (TS): We have many years of service in our company: many employees have been with the company for more than 25–30 years and, in some cases, their fathers worked for us as well. I am the fifth-generation managing director. Today, we want to take a step toward industrial production and are fighting against habits — things that we have "always done this way." Our projects are getting bigger. We need lean production to cope with this growth. I noticed that, with the means currently at my disposal, I was making progress too slowly. I've been thinking about looking for external support for a while. In 2021, my production manager was at the WEINMANN Treff, got to know SCHULER Consulting and came back all bright-eyed. That was the impulse for me to tackle the issue now.
Mr. Postulart, your project with Schütt is about making production processes "leaner" and therefore increasing productivity during operation. How did you start the project?
Michael Postulart (MP): Our first conversation was about the fact that the new system did not achieve the desired performance in production. At Schütt, there is a four-table system with a WALLTEQ bridge and semi-automatic blow-in insulation. This was the trigger for a visit to the site, which allowed the "Lean" project to get underway. We dropped in with a small team from SCHULER to investigate why the machine had so much downtime. First of all, we gained an overview of glue-laminated wood production and wood frame construction. We then analyzed the wood frame construction production and performed multimoment studies. We used spaghetti diagrams to analyze the distances and routes covered by the production staff and found that the staff did a lot of "unnecessary" walking about during the day, for example to obtain tools, and therefore were not standing at the machine at these times. Reducing walking times for employees was the first step toward achieving short-term improvements in productivity. Mr. Schütt was satisfied with our work, so we then developed a catalog of improvement measures for the entire production line, which we are now gradually working through.
Mr. Schütt, there are still some changes to be made to the production processes. How are your employees reacting to these? How do you take your team with you when making these changes?
TS: My people are incredibly hard-working. We push a lot through, but you can't overstep the mark. From a certain point, you have to initiate a change process — also because you don't want to overwhelm your own people. What you shouldn't do is go into production with someone from outside and not inform the employees about what is going on. You have to take the employees with you and talk to them beforehand about who is coming and what is happening. Otherwise, they become profoundly wary and worry about whether, for example, their job is going to be streamlined away. This lines up well with Mr. Postulart and our team. He speaks the language of the employees, involves them and motivates them to participate in the change process. That's how we get things going. It is important that we take up these ideas and then implement them. At our company, this happens during the entire workflow. These things are not rocket science, but they are often not implemented. The external support helps you to commit to tackling these issues and giving yourself a timeframe to do so.
Mr. Postulart, how do you involve employees in the project specifically?
MP: From manual work to industry — this is a change of mindset. It requires acceptance and an understanding of what lean production can look like. As Mr. Schütt says, it is extremely important to take the employees with you and celebrate small successes with them. At the heart of this is one simple question: "What can we do to simplify your daily routine?" To answer this, we held a workshop and immediately put the findings into practice. The result is a mobile snipping unit that can make work in production more flexible. For me, it is important that everyone sees that they can make a difference by getting involved. So, we started with a small idea and implemented it. This was a small but important success that we achieved together.
What "small successes" have you already achieved on the road to industrial production? And what's next?
TS: One of the first improvements in production was an upright store. We used to prop the walls up in a more or less makeshift way. Now we have a central place for further processing steps and can finish the façades and install the windows.
MP: The upright store is an in-house design from Schütt. It enabled us to optimize the material flow before loading. One goal of the project is to optimize the general material flow in production — to optimize the use of storage areas and logistics as a whole.
What optimization potential is there in the area of logistics?
TS: In the last two years, the work has been defined by supply bottlenecks. We purchased a lot of material and actually "misused" our best hall as a warehouse. We want to change that now. Our people have to walk excessive routes to get their material. We want to improve the whole topic of logistics in the long term by hiring a logistics employee. In the short term, we can already reduce long travel routes by providing additional tools. This is more favorable than employees walking time.
MP: The logistics employee will take care of providing the material. This will mean that an employee who is currently standing at the frame work station does not "just" unload a truck, or that a workpiece is carried to the snipping station manually. These are a number of initial small topics for improving the material flow and the utilization of storage areas. We will then focus on the big strategic things.
TS: The collaboration with SCHULER is well defined, we are progressing at a good pace with a clear vision and want to work together over the long term. We want to expand the project even further and go through the same processes in the glue hall. A conversion is planned and then we will relocate the warehouse logistics.
Mr. Schütt, the optimizations in production are just one part of the many changes that are coming to your company. How do you manage to stay on top of these topics?
TS: I am well informed about what is happening in the industry through association work and participation in the timber construction forum, etc. — these are things that my employees may not necessarily be aware of. It is very important that you pass on your own ideas for company development and market development to your employees. That's why we conjured up a vision for the whole company two years ago and created a PMO (Project Management Office) position to accompany the process. This process affects the whole company. There are various working groups in modules that come together every 14 days, and we carry out a "deep dive" every 3 months. The work results from these groups are regularly passed on to all employees. No one can say that they don't know what is happening in our company.
What would you recommend today to your colleagues in the industry who also want to industrialize their business?
TS: First of all, I can recommend to anyone who wants to automate their production to involve SCHULER immediately. The clearer the task, the easier it is to plan your production to the last detail. When I look back, it's clear that we did not have a clear product image. We don't have the single-family houses that we once knew. Today, we are building 80 houses and now want to increase that to 120 or 150. In the commercial sector, we offer different floor heights. These are special constructions. So, the focus for our WEINMANN system was not exactly clear. We started by buying the system and then following up with the consultation step. There are also other ways of doing this. I also think that the advice provided by The SCHULER Company EKG is excellent. It is suitable for anyone who is thinking about where they are. With the consulting service, you know what you are paying for and already have a proper catalog of measures. I can only recommend maintaining the external support so that your implementations can be retained.
Videos
Please confirm that when you use YouTube, data such as your IP address, browser identifier and similar may be transmitted to Google.
» Privacy Policy
Producing more and more efficiently: SCHULER Consulting supports the Schütt company in production and process optimisation.