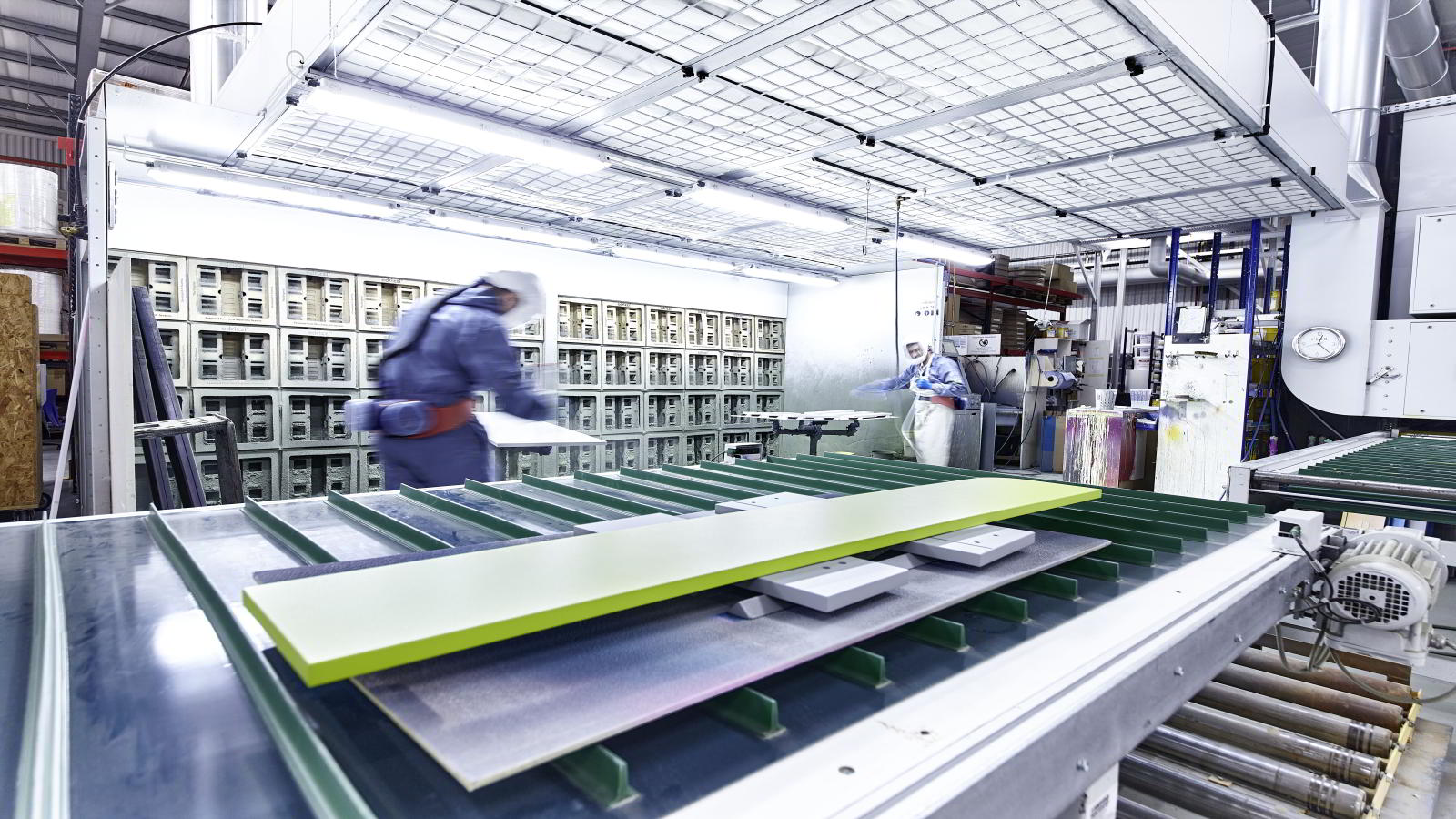
In the first part of this article, our software consultants Klaus Fickler and Luca Föhn gave practical tips for SMEs and industrial manufacturers on software selection. In the second part of our mini-series, Professor Holly Ott from the Faculty of Wood Technology at Rosenheim University of Applied Sciences and Klaus Fickler report on a joint software project at Möbelfabrik Rudolf in Hesse. The project team supported the family-owned company in selecting a new ERP system to replace the LIGNOS-M software in the future.
Medium-sized furniture manufacturers in Germany have been facing the challenge of adapting their production to the demand for highly individualised furniture for years. Customers are increasingly demanding individuality and new trends. Many furniture manufacturers recognise the potential of serving a fashion-driven market. The mutual understanding of market and manufacturer means that producers have to maintain a constant flow of new collections and offer a growing range of finishes and variants. This puts them in competition with highly standardised companies whose business model is based on a limited range and modularised, low-cost furniture pieces. The highly standardised furniture manufacturers often produce at lower-cost production locations, such as in Eastern Europe. Many German medium-sized producers are therefore increasingly focusing on quality, customisation and sustainability in order to be able to compete with the low prices.
Such a "mass customisation" model requires manufacturing individual components quickly and efficiently in order to deliver customised orders on time. Over the last 10 years, many SMEs have made the important decision to reduce their inventory and move to batch size 1 production. This requires flexible production and complex material and information flows. The choice of software systems to support this change and future developments for SMEs significantly shapes the company: from customer to employee, from order entry to machine, from production to assembly to shipping - new software can digitalise and accelerate company processes. SMEs often go in search of software without taking into account the diverse and sometimes complex processes in their company as a whole. In particular, the upstream and downstream processes are often neglected. As a result, project costs skyrocket and the communication effort, for example with employees, increases. In the first part of this article in issue 04, you can read how to find the right software step by step to move the company forward. Holly Ott and Klaus Fickler accompanied Möbelfabrik Rudolf und Sohn in such a selection process for a new ERP system.
Tradition meets future: The Friedrich Rudolf und Sohn furniture factory from Hesse
The furniture factory Friedrich Rudolf und Sohn, based in Schlüchtern (Hesse), has been in existence for over 125 years and is now run by the fourth generation of the family, Karl Friedrich Rudolf. Since 1895, the furniture factory has been producing individual living solutions for life in small spaces. More than 120 employees belong to the company, which attaches particular importance to sustainable products and manufacturing processes. For example, the furniture manufacturer uses water-based lacquers and relies on short delivery routes and production in Germany. In recent years, the company has invested in new machines and production software and initiated the conversion of production to batch size 1. Today, the product portfolio includes youth, flat, hallway, contract and home office furniture made of derived timber products, which is mainly sold in German-speaking countries through specialist dealers. The product quality and manufacturing standards are regularly independently tested and certified. Among many other awards, the company bears the climate label "Climate Neutral Furniture Manufacturer" and the "Golden M" of the DGM (German Furniture Quality Association).
With the discontinuation of LIGNOS-M in 2018, Rudolf re-evaluated its data flow and looked at the options for a replacement ERP system. The ERP system LIGNOS-M had been in use at the Rudolf company since 1986. The system had been developed specifically for furniture production and made it possible to store a limited number of variants for each part produced. The aim of the joint software project with Schuler Consulting and TH Rosenheim was to find an ERP system that could replace LIGNOS-M. The project was completed in March 2007. Through the cooperation of TH Rosenheim and Schuler Consulting, Möbelfabrik Rudolf benefited from the bundled industry know-how from research, industry and over 60 years of consulting expertise in the international wood and furniture industry.
Understanding the current situation: A new solution for LIGNOS-M
At the beginning of the project, the focus was on analysing the ACTUAL situation. For this purpose, the team looked at the current process landscape of the Rudolf company and analysed the flow of information from order acquisition with the help of Furnplan to delivery to the customer. In a flow chart (Fig. 1), they visualised the path of the data via the various IT systems from order entry to dispatch. This made visible which interfaces the current ERP system has to other software systems such as the production control system ControllerMES (HOMAG) or to other, non-production-related work steps such as financial accounting.
For the furniture manufacturer with highly variant products, the management of article components and order entry was particularly relevant here: To handle the variants, the orders are entered using the HOMAG solution OE ("Order Entry"). Here, each article of a customer order is entered into the system with its specific characteristics (dimensions, colour, handles, edges, etc.). The order entry software generates the customer-specific parts list from a maximum parts list. A route planning takes into account the delivery date and the customer's request; then the production is planned in an optimised way. The sales order, including the item positions and the specific parts lists, is then automatically transferred to LIGNOS-M, which generates an order confirmation to the customer. LIGNOS-M is able to track five variants per part via a part identification number and map them with its characteristics.
Given the wide range of colours, handles and dimensions, a single cabinet from Möbelfabrik Rudolf can have thousands of variants. This is a major challenge for handling the flow of materials and information. With the large number of combinations of colours and dimensions, only frequently-used parts are produced in stock; all other parts are custom-made, combined into a commission-based order and delivered. For this purpose, Möbelfabrik Rudolf considers both make-to-stock (MTS, strong runner) and make-to-order (MTO, weak runner) models in its production. For MTS parts, which are produced or purchased regularly and in high quantities, an automated high-bay warehouse is managed on site. The ERP system displays the current stocks of all MTS and Purchase-To-Stock (PTS) parts or the available stock range at any time. These are manufactured, purchased and stored "in batches" in the appropriate batch sizes. The slow-moving items are either manufactured in the MTO model or procured Purchase-To-Order (PTO).
Thus, there are two principles in MRP: The MTS parts are manufactured with defined lot sizes, the PTS parts are procured in larger quantities. The MTO parts are manufactured in the exact order-specific quantity, the PTO parts are procured individually. In addition, MTO production and PTO procurement are subject to the "tour scheduling" control loop. From a manufacturing perspective, there are consequently two manufacturing routes in production. The MTS and MTO parts run through two different lines, whose manufacturing documents must be set up separately accordingly. Before assembly, the MTS, MTO, PTS and PTO components and fittings must be picked accordingly. On this basis, the order-related assembly (ATO = Assembly-To-Order) and the assembly of the packages (RTA = Ready-To-Assemble) then take place.
Ninety per cent of the variants and, in terms of quantity, about half of the parts consist of batch size 1 parts, which are manufactured individually for the order in time for the delivery date. Both production methods are justified at Möbelfabrik Rudolf. The challenge for the medium-sized producer is to combine the different manufacturing processes and synchronise their processing via the IT systems. To start the production process at Rudolf, the order information must be transferred to the company's IT systems, as shown in the flow chart.
The example of the Rudolf furniture factory illustrates that the IT landscape of a company must support the individuality of production and the product range. At the Rudolf company, this is achieved by linking their ERP system to the OE and the production control system cMES, which can be expanded modularly and "grows" with the company. For the production of highly variant furniture, this is a solid solution for the Rudolf furniture factory.
Drawing up specifications: Requirements for the new ERP system
A key requirement for the new ERP system is to ensure the previous flow of information. This means ensuring that all data at the interfaces from upstream IT systems enters the ERP system and is passed on to downstream systems. Since the ERP system is connected to many other IT systems, this requires in-depth knowledge of the current software landscape as well as of possible future developments of the company, for example the manufacturing philosophy.
In the specific case at Möbelfabrik Rudolf, the management of article components is particularly relevant. With LIGNOS-M it was possible to store the variants in the ERP system and thus to see directly which part is produced or purchased as MTO/PTO and which part as MTS/PTS. Without a variant-capable ERP system, the MTO parts from the OE are transferred directly to the cMES and not recorded in the ERP system. Since each component is described in OE via its variant and this information is stored in a special parts list, the central question for Rudolf was whether the new ERP system must be able to map all variants if variant-capable software is already in use.
Since all variants can already be mapped via OE and cMES, time-consuming and cost-intensive double data maintenance can be avoided with a non-variant-capable ERP system. From a cost and effort perspective, it is more sustainable to use existing data models. In production planning, information on whether a part is manufactured as an MTO or MTS part is crucial in order to react flexibly to market demands. A part that is purchased or manufactured in small quantities today (PTO/MTO) can "mutate" into a strong runner tomorrow due to increased demand, which is now produced in stock. The same applies to parts that are no longer in high demand, so that an MTS part can become an MTO part. So how can this flexibility be ensured for production planning with two different manufacturing processes without using a variant-capable ERP system?
Since each variant is recorded in the part description in OE, a flowing production can be ensured with the connection of the cMES and OE even without a variant-capable ERP system. The description of the variant is saved with all the necessary information in an order-related special parts list. This list provides information about the required quantity of a variant in a certain time and can serve as a basis for decisions in production planning. In this way, it is possible - even without a variant-capable ERP system - to decide flexibly on the basis of the already existing data model in OE which production route a part will follow in the future. This involves less cost and effort than creating a new data model for all variants in a new variant-capable ERP system.
In addition to the optimal adaptation to the manufacturing philosophy, a future-proof system that meets the requirement criteria as far as possible is important when selecting a new ERP system for the cabinet furniture manufacturer. In addition to the "hard facts" such as interface compatibility and the cost framework, the project team defined the "soft facts" in the specifications, such as the references as well as the consulting and problem-solving competence of the potential software supplier.
With the bundled information in the specifications, the search for possible software providers began. During the market research, the project team was able to narrow down the pre-selection to potential suppliers that fit well with Rudolf's requirements. They sent the specifications to these suppliers for a response. All the suppliers contacted completed the specifications, so a smaller group was invited for the next round of evaluation, the product presentation. The final decision for an ERP supplier is still pending at the time of writing (June 2021).
Thinking about tomorrow today: automation and IT trends
The new ERP system has the potential to support Rudolf in many ways - not only in the complex production landscape of MTS and MTO parts, which has to manage planning and production for two completely different production routes. This requires parallel production lines, a warehouse for MTS parts and a sophisticated picking step to combine the MTS and MTO parts for assembly. The creation of the specifications allowed the company to think about and redesign its processes and procedures to become leaner and more efficient with meaningful, networked IT systems. This also allowed for considerations regarding the digitalisation of processes, for example for better data collection from the production flow as well as less paper in production and administration. The new ERP system gives Möbelfabrik Rudolf more customisation options and increases the speed of communication with the customer.
With the software project, Möbelfabrik Rudolf has taken another important step towards the future. But the renewal of the ERP system is not enough - the owners continue to deal with the development of the company and want to equip the family business for the future. Because they know: When choosing software, it is not only current product trends that need to be considered, but also the development of IT systems themselves. For example, cloud-based software-as-a-service models increasingly offer the furniture industry more flexibility in application and usage-based billing. Furthermore, the Rudolf company is concerned with the question of how the topic of sustainability will develop in the industry. Here, the factory sees great potential to make furniture transport more sustainable, from packaging to transport itself. For this reason, it is involved as a pilot company in a research project of the TH Rosenheim, which will start in 2022.
About the authors:
Klaus Fickler: In his many years as a software consultant in the woodworking and furniture industry, Klaus Fickler has already implemented numerous software selection and process optimisation projects. Formerly active for HOMAG in ERP and PPS implementation, Klaus Fickler has now been working for SCHULER Consulting for over 25 years. As an industry expert and software specialist, he now mainly carries out projects in the MES and ERP environment at SCHULER. He also advises companies on the topic of Industry 4.0 and carries out complex information flow analyses, from the point of sales to production.
Prof. Dr. Holly Ott: After receiving her doctorate in electrical engineering from the University of Virgina, Holly Ott worked for Siemens, IBM, Motorola and Infineon, among others, in the USA, Europe and Asia. In 2014, she was appointed Professor of Industrial Engineering at the Bavarian Business School. The following year, she developed one of the world's leading online learning programmes for TU München and the MOOC provider edX. Since 2020, she has been Professor of Production Management and Operational IT Systems at the Faculty of Wood Technology and Construction at Rosenheim University of Applied Sciences.